Industrial Curtain Track System & Hardware
Food Grade & Processing Curtains
The food industry has long been one that uses industrial curtains with industrial curtain track hardware for a variety of reasons. From equipment wash down to allergen containment, there are many applications for food processing curtains in the food arena. The industrial curtain track system is used for food applications which have to meet stringent criteria to avoid bacterial growth and stay safe for incidental contact with food products. While AmCraft has offered food grade curtains for many years, a more recent offering of ours is the Clean Glide track system. This is an industrial curtain track system which was custom engineered by AmCraft and our track manufacturing partner specifically to fit the needs of the food industry.
In early 2020, between the worldwide focus on hygiene and safety and the strains put on food manufacturing sectors everywhere, it became clear to us at AmCraft that we would need to offer a fully food grade track option to sell with our food grade curtains. The responses we received were that the food processing curtains were great, but if we could not hang them, and if they could not retract, in a food safe way, then they could not be used.
Click here to learn more about Food Grade Track System & Food Grade Curtains
Food Grade Tracking System
We stared by looking at our competitors. A handful offered a
food grade tracking system,
but many did not. Of those that did, the systems looked either very large and clunky (potentially overkill for what was needed) or almost too small to be sturdy and effective. Here at AmCraft, we strive to create the best products possible, and we did not feel that what was already out there fit that bill. So, we did what we do best, we went back to the drawing board, and recreated and improved the wheel, so to speak.
It stared with our director of sales and our most knowledgeable product engineer. They worked with our current track system manufacturer for months to determine how this food grade track needed to look, function, and its ideal price point. Their combination of knowledge about what customers needed and what was possible from an engineering point of view were instrumental is deriving the Clean Glide track system.
In terms of look, the key tenet was to provide a pipe size that was middle ground for what was out there already. Nothing too slim and flimsy, our products are built to last. While at the same time, trying to keep the pipe size away from being overkill- thus driving cost up unnecessarily.
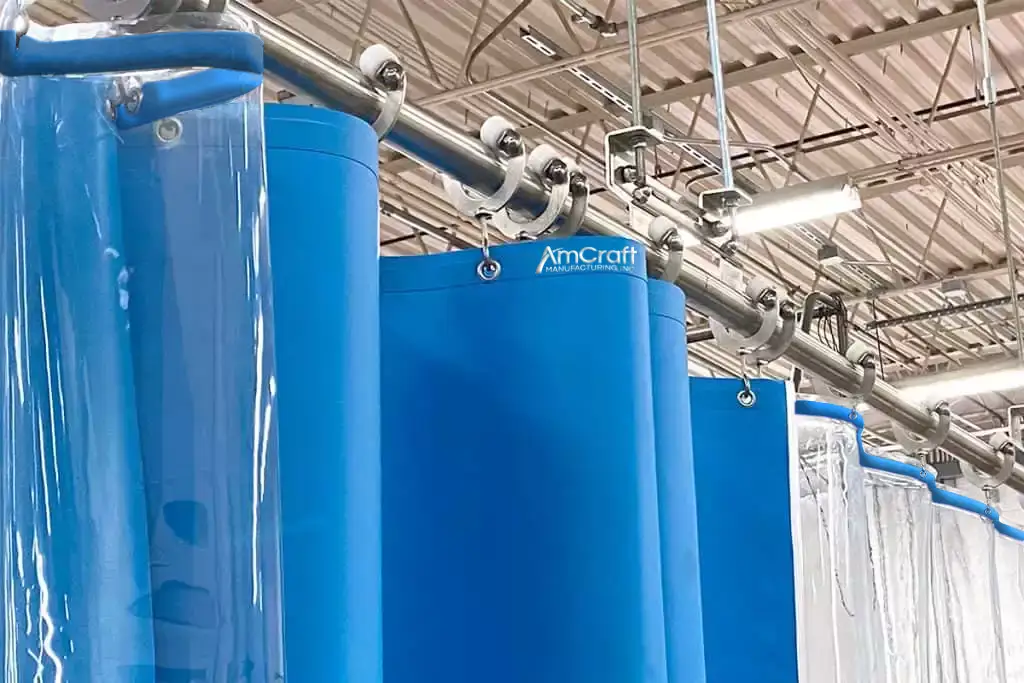
Once the perfect tube size was determined, the next hurdle was how to connect the track pieces together. This was a question of aesthetics, but also of function. A food grade track needs to have minimal horizontal surfaces, so that contaminants do not have a place to land, collect, or grow. Additionally, the connection point of one piece of tube track to another needs to be completely sealed for the same reason. It was determined that a combination of a custom designed internal connection, sealed with FDA grade silicone sealant, as well as a diagonally slanted external bracket would be the best connection method. These two connection methods, when used together, check all the boxes to keep the track securely fastened together and also completely FDA compliant.
The culmination of all of these efforts is that AmCraft can offer a uniquely engineered track system that is of high quality, meets food grade standards, functions flawlessly, and retails at a consumer friendly price point. The Clean Glide track system is consistent in its quality with all of the products that AmCraft offers. It has proven to be a very popular track system option, and is a prime example of what happens when creativity, ingenuity, and necessity meet.